www.engineering-japan.com
03
'18
Written on Modified on
機械加工の先を見据えた包括的工具劣化分析
切削工具は、機械切削工程における基本的要素です。工具の選択方法および適用方法によっては、機械加工の生産性が最大化することもあれば、反対に製造のボトルネックになることもあります。その多くは、全体的な製造工程に対して工具の使用をどう管理するかによって異なります。
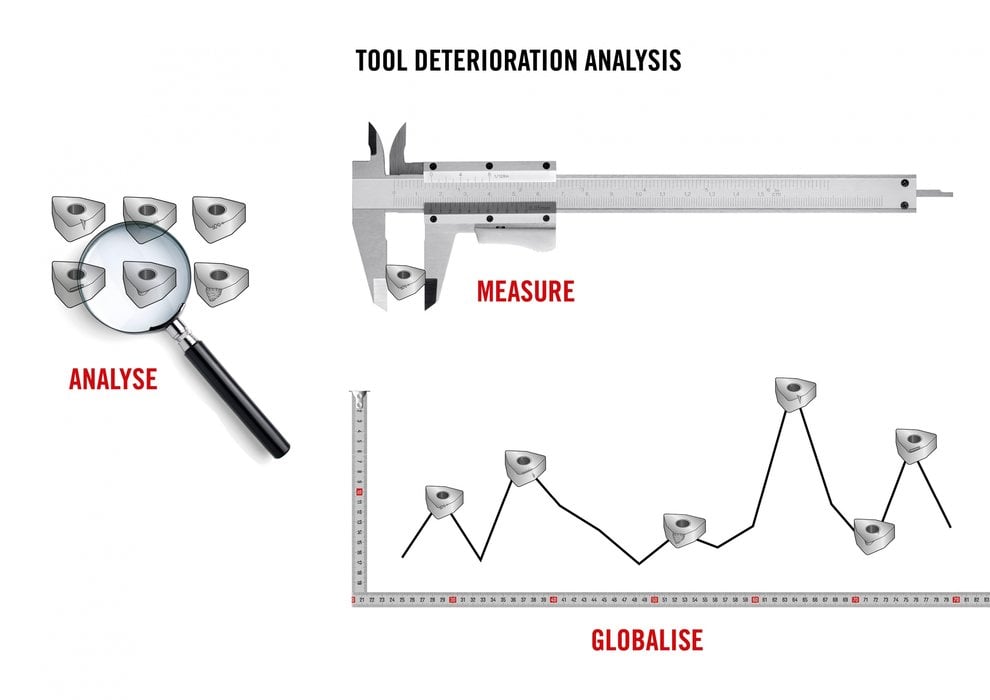
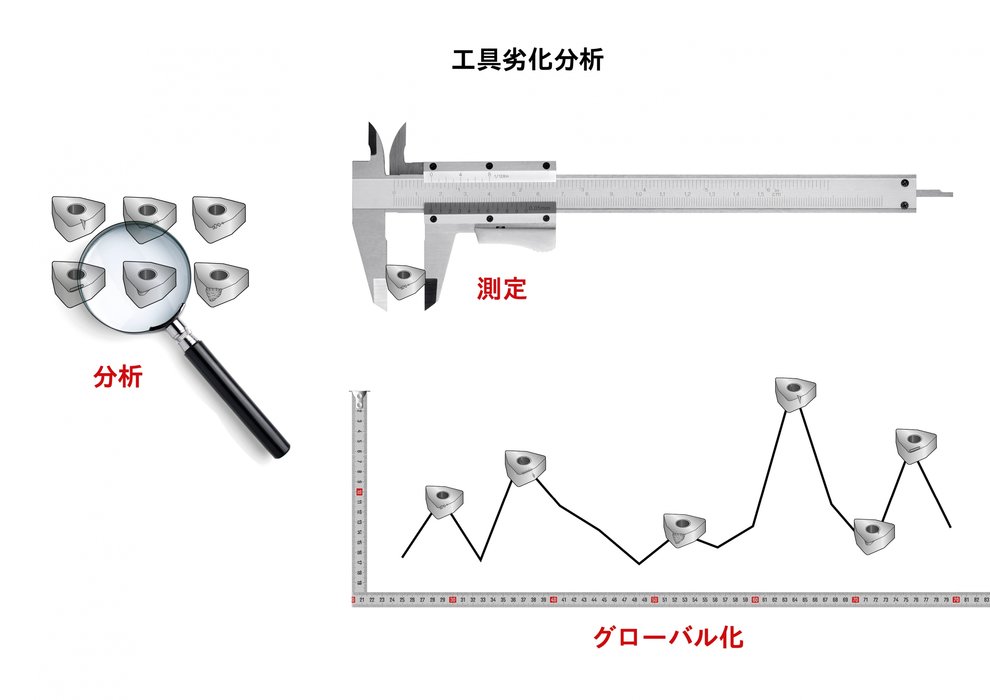
工具摩耗について
図 1
切削工具はその性質上、消耗品です。摩耗すれば、効率的には使えなくなります。金属切削工具の管理に関する一般的な方法では、摩耗分析のみを使い、主として工具の材質、形状、用途の各条件を操作して、選択した作業における部品の生産量と工具の寿命を向上します。ただし、施設の全体的な製造工程の効率を最大化するには、工具の摩耗に加えて、多種多様な要素を考慮する必要があります。全体的つまり「包括的」な製造工程を考慮して、切削工具の摩耗(より広義には工具の劣化)を検査することが不可欠です。
包括的工具劣化分析(GTDA)では、工具の摩耗を測定するという基本的なことだけでなく、工具を使用した時間、摩耗以外の問題点、生産経済性、加工現場の組織、人員の心構えと条件、価値ストリーム管理、トータルの製造コストなど、工具に関連するさまざまな要素が考慮されます。GTDA は、無作為に選択した加工現場で使用されている数多くの切削工具の定期的な評価をベースにしており、施設の全体的な生産活動にどう影響しているかを包括的に把握します。
包括的な製造工程
工具の摩耗の調査は多くの場合、特定の機械加工作業に使用されている 1 つの工具に限定されています。ただし、最大限のメリットを得るには、施設の製造工程で使用されているすべての工具について、摩耗または劣化を調査することが不可欠です。製造工程(図 2)では、最初に原材料の入手と、人的資源の活用、技術リソース、資本投資などの計画を行います。続いて価値付加活動および価値実現活動を行いますが、費用、時間、知的リソースを無駄にして、最終的に部品の品質と歩留まりを下げる原因となる摩耗を発生させる事象によって制約を受ける可能性があります。生産量は、部品の品質、必要な数量、所定の生産時間、コストによって測定します。
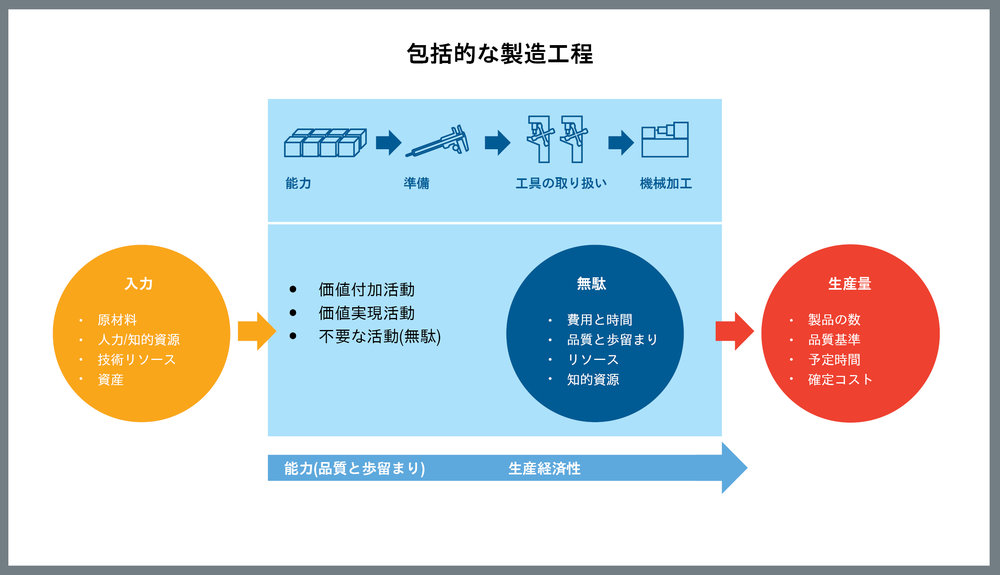
製造工程
図 2
製造工程の進化
工具寿命の分析および予測に使用する方法は、工具をどのように使用しているかによって異なります。製造方法は、数百年を経て、個々の品目を職人レベルで製造する方式から、標準化された部品を大量生産する方式へと進化しました。製造方法が改善されたことで、似た部品を大量に製造(大量少品種(HVLM))できる第 2 世代の大量生産が始まりました。直近では、デジタル技術をプログラミング、工作機械の制御、被削材処理システムに適用して、コスト効率が高く、多品種少量(HMLV)生産が可能な第 3 世代の大量生産が行われています。
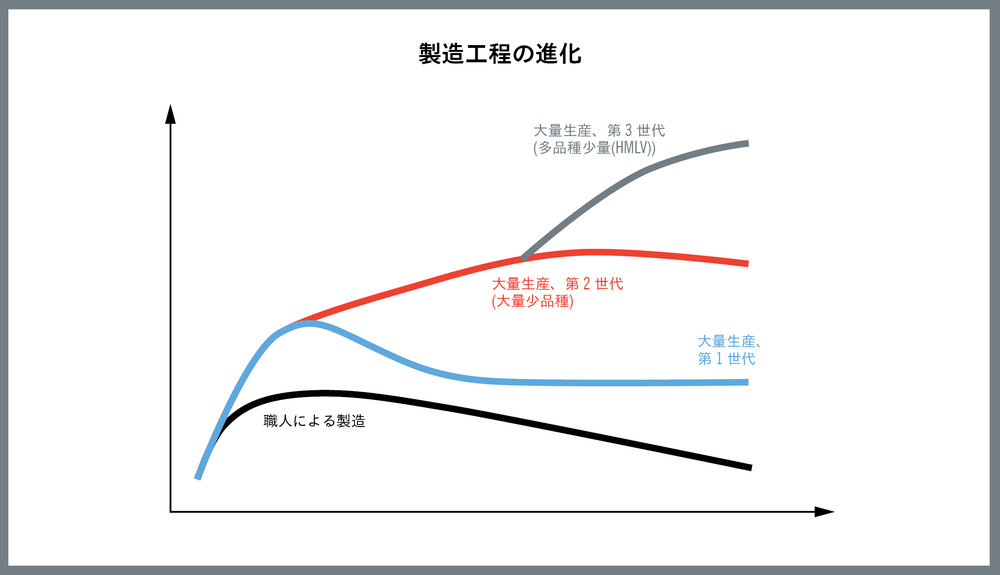
製造工程の進化
図 3
性能に関する主な課題が、コストおよび時間の効率向上、特定の最小限の品質と特定レベルの歩留まりの達成であることに変わりありませんが、第 2 世代および第 3 世代の大量生産技術では別のアプローチで工具寿命を分析する必要があります。第 2 世代の HVLM シナリオにおいては、同じ工具と同じ種類の切削工具を使って、数日、数か月、あるいは数年間、同じ被削材から同じ部品を製造します。この場合、工具寿命の管理は比較的単純です。加工現場の担当者が試作品を使って試験生産し、理想的な平均工具寿命を算出します。次に、部品の予定製造数量を各工具の想定寿命で割ります。
加工現場は、工具の推定寿命に関する一貫したデータがあれば、工具を最大限に使用し、継続的な生産をサポートする工具交換を計画できます。ただし、HVLM 製造方法は急速に衰退しつつあります。メーカーは、部品の在庫と需要のバランスをとり、進行中の技術変化に対応するため、製造する部品の数を減らし、製造工程を長期間変更しません。
同時に、第 3 世代の HMLV 大量生産戦略が採用されるようになっています。迅速に調整可能な HMLV 工程は、在庫および技術に関する現代の目標にうまく適合していますが、計画工程ははるかに複雑になっています。部品を 10 個製造したあとで 2 個や 5 個といった部品ロットを製造したり、場合によっては部品を 1 つ製造するということもあります。被削材種は鋼からアルミニウム、さらにはチタンに、部品の形状は単純なものから複雑なものへと変更されます。試験で工具寿命を算出する時間的余裕などありません。
ワークショップではこのような場合、工具の想定寿命について控えめに推測を行い、大事をとって製造ごとに新しい工具を使用するため、工具は効率的に使用できる寿命に達するよりかなり前に廃棄されます。工具摩耗の分析と予測に関してより包括的な方法を採用すれば、切削工具の能力の無駄を最小限に抑えることができます。
歩留まり率は 100%かゼロ
HMLV 製造方法は急速に変化しており、機械加工作業の歩留まり率を高くすることがますます困難になっています。長期間の HVLM 製造の場合は、試験と調整によって 90%後半の歩留まり率を実現できますが、HMLV における歩留まりは 2 つに 1 つです。単一の部品を無駄なく製造すれば歩留まり率は 100%ですが、製造された部品の品質が悪かったり、被削材が無駄になると、歩留まり率はゼロです。
品質、コスト、時間効率に対する要求は変わりませんが、初回の歩留まりは最重要要件になっています。この場合、工具の破損がないようにすることが最も重要な考慮事項だと思われます。短期的には工具の摩耗を心配する必要性が低くなり、無理のない範囲で、より積極的かつ生産的な切削の条件を適用できるというメリットがあります。
職人技と人の関与
長期間で、変更の少ない HVLM 製造では、製造工程に人が関与する重要性が最小限になる傾向があります 。製造期間が長い場合は、基本的に操作は自動化されます。部品を切り替えるたびにオペレータが関与する場合であっても、繰り返し行うという性質上、オペレータやプログラマの影響が軽視されます。柔軟性は不要となり、敬遠されることさえあります。
逆に変更が速い HMLV シナリオでは、工程における人の役割は重要です。継続的な部品の切り替えや HMLV 加工の切削条件の特性に効率的に対応するには、創造性と柔軟性をともなう従来の職人技が必要です。
結果の前に工程を重視
製造工程分析における作業の多くは、工具寿命と部品の生産量に関する最終結果の確認を重視し、工程そのものを徹底的に調べることはしません。切削工具に関係していても、工具寿命には直接関係しない問題は見逃され、製造のボトルネックになることがあります。たとえば、一般的にバリは工具寿命に関係しませんが 、バリが発生すると製造工程の妨げになります。別の工程を作ってバリを取り除く必要があるからです。
ただし、バリの形成は工具形状および用途条件に関係するため、工具劣化分析において考慮する必要があります。工具の破損は、多くの場合工具の摩耗には関係しない別の問題ですが、工具の素材、形状、用途条件 、工作機械の要素が関係します。
作業効率の要素
無駄、硬直化、ばらつきをなくすことが、製造効率の基本的要素です。包括的な工具劣化分析では、作業効率に関する 5 つの要素を考慮します。
第 1 に、機械加工工程全体と、機械加工作業および被削材種との関係を十分に把握することが不可欠です。第 2 に、製造戦略などの施策を通じて、無駄を削減することに留意する必要があります。第 3 に、生産経済性のコンセプトを導入し、収益性を確保します。第 4 に、歩留まり率の目標を、生産量と部品の種類を考慮して考える必要があります。柔軟性を最大限に高めることを、ボトルネックを最小限に抑える 1 つの方法と考える必要がありますが、部品の公差を一貫させるために、ばらつきを制御する必要があります。最後に、固有で替えがきかない人的リソースから得られるメリットを最大限得られるように、製造要員の価値を強調する必要があります。
工具の摩耗以外の考慮事項
工具の包括的分析では、売上原価(COGS)の合計、シングル段取り(SMED)分析、価値ストリーム管理(VSM)の結果、総合設備効率(OEE)の比率における工具の役割を分析して、チップ刃先の摩耗の初回の測定を補完します。
工具関連の最も基本的な経済的考慮事項は、言うまでもなく工具関連のコストです。図 4 は、機械加工工程における各種要素のコストを示しています。各コストを合計したのが COGS です。このデータを使って、生産コストの各種要素を比較し、作業の収益性を大幅に上げるコスト削減の候補を見つけます。
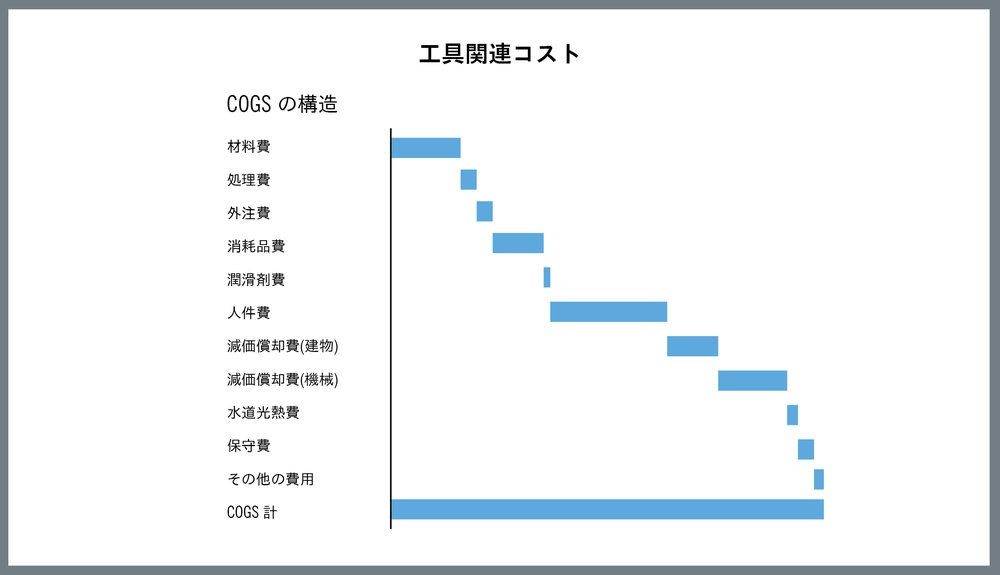
工具コストと効率
図 4
工具に関連するもう 1 つの経済的要素として、工具のコスト時間があります。実際に機械加工作業を行う以外の、工具の操作に必要な時間のことです。工具の切り替えや設定に必要な時間を SMED 分析技術を使って分析します。これにより、工具の入手と整理、取り付け、工作機械へのプログラムの読み込みなど、工具の摩耗と交換によるコスト以外のコストも確認できます。
OEE により、製造時間のうち効率的に使われたのはどれだけだったのかを算出します。OEE 分析により、損失を見つけ、進捗状況をベンチマークし、無駄をなくして生産性を向上します。生産に使用可能な合計時間を確認し、予定のダウンタイム、予定外の故障、切り替え、軽微な停止、速度低下、スクラップ、再加工を差し引いて、効果的な機械加工時間を算出します(使用可能な合計時間の割合で表す)。OEE は 100%が理想的ですが、現実には達成不可能な目標です。100%は、指定した品質で、できるだけ速く、時間を無駄にせずに部品を作ることを意味しています。
VSM 分析により、製造工程におけるすべての要素間で、性能改善のバランスをとる必要があることが分かります。図 5 は、システムの要素 1 つの性能を向上(その他の要素はそのまま)したときの効果を模式化したものです。複数の人でボートを漕いでいる様子を想像してみてください。1 人だけ精を出しても、ボート全体の性能は損なわれてしまいます。
全体でバランスのとれた製造作業を達成し、維持するには、生産量とばらつき、被削材種の特性、部品の形状、加工工具および取り付けの要件などの考慮事項との関係を考慮して、工程の部品の改善を実現する必要があります。
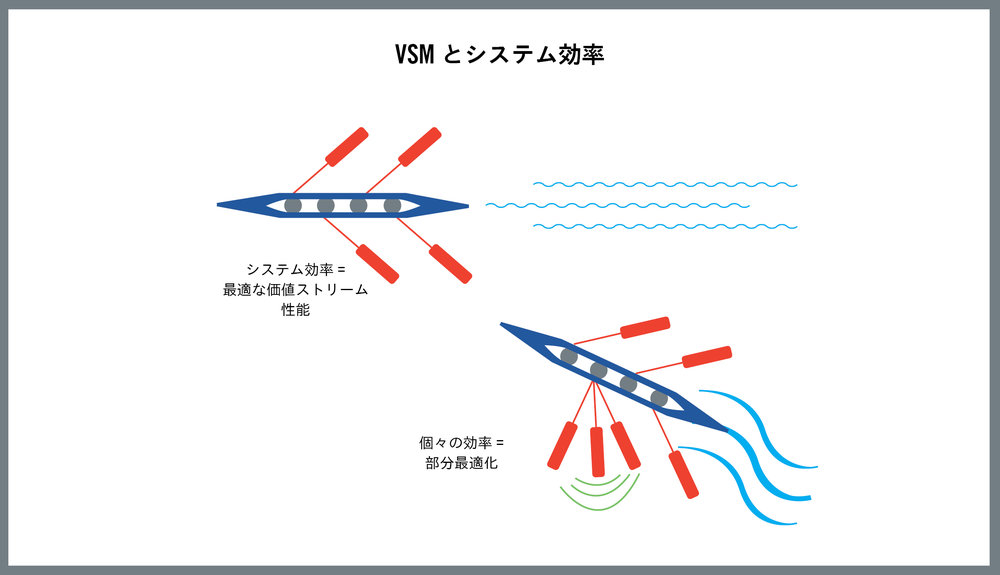
VSMとシステム効率
図 5
包括的工具劣化分析
GTDA は基本的にシンプルな工程です。加工現場の各所で使用されている工具から無作為に選んだ多数の工具の切れ刃を、一度に 1 枚ずつ検証し、どの刃が摩耗しているかを確認します。摩耗は種類と程度に従って分類します。従来の工具摩耗分析では、1 つの工具の 1 回の操作で行います。GTDA では、工具の摩耗と工具関連のその他の問題に関する情報を加工現場全体から集め、COGS、SMED、VSM、OEE などの分析ツールを使って、プログラム改善の計画と導入に役立つ詳細なデータを作成します。
GTDA を有効活用するには、加工現場で訓練を行って GTDA プログラムを開始します。また、工具を継続的に観察し、データを定期的に分析することも同じように重要です。正直なところ、これとは別の訓練も必要です。加工現場は、分析結果を誠実かつ客観的に受け入れ、分析で分かったことに基づいて積極的に対策を実施する必要があります。この際、加工現場のこれまでのやり方や方針、工具適用条件についてサポートされていない意見は考慮しません。
結論
工具の摩耗を避けることは不可能であり、最適な機械加工作業を実現するにはその管理が不可欠ですが、工具の摩耗は、施設の全体的な製造工程の効率性に対する数多くの切削工具の影響の 1 つに過ぎません。GTDA では、単独工具の摩耗分析だけでなく、加工現場におけるすべての工具や、切削工程以外の工具に関連する重大な影響も幅広く対象としています。
補足:
GTDA: 理由と方法
個別の部品を大量生産していた時代の最盛期には、工具寿命と部品の生産量を最大化するために、工具の摩耗を測定して処理し、バランスをとることしかしていませんでした。注文生産に近い部品をよりジャストインタイムで製造する方式へと製造戦略が進化するにつれ、工具の摩耗が単独で製造工程全体の中心的な要素となることはなくなってきました。
セコ・ツールズのコンサルティングサービスは、製造工程における進化を継続的に分析し、製造産業における絶え間ない変更に対応する「NEXT STEP」生産モデルを構築しました(図 6)。NEXT STEP モデルは、機械加工における 4 つの重要な標準(対コスト効果、時間効率、品質、歩留まり)に基づいています。NEXT STEP を導入することにより、メーカーは無駄発生の分析、機械加工工程技術、工具および被削材種の科学、生産の経済性と歩留まり、作業における人やリーダーシップの重要な役割を通じて、自社の機械加工標準を設定し、適合することができます。
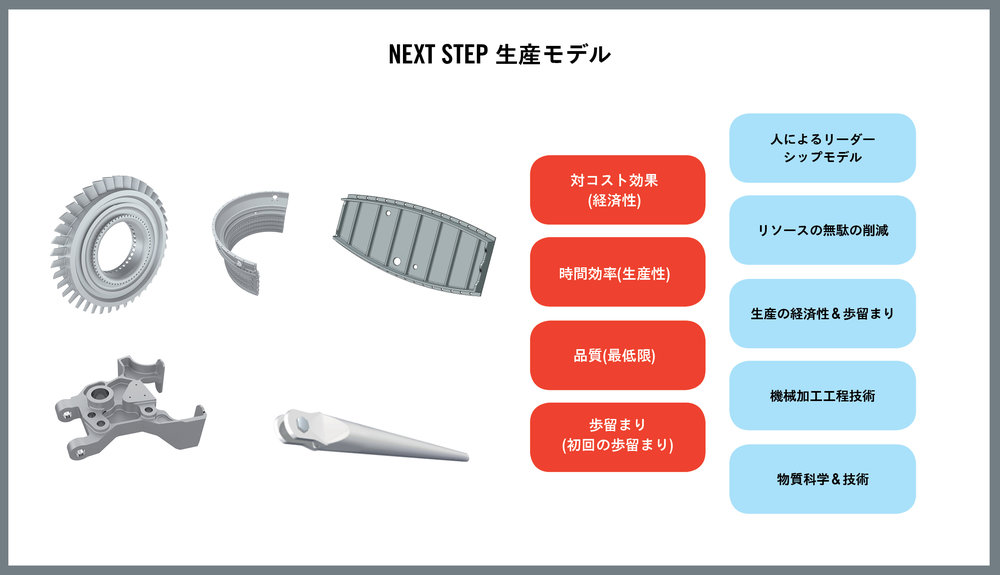
次世代の製造工程
図 6
包括的工具劣化分析(図 7)は、製造工程を全体的に評価して改善するうえでの主要な構成要素です。メーカーは、工具を無作為に選択して調べ(施設の機械加工領域すべてをカバー)、各種の製造計測を適用することで、機械加工工程全体における工具の役割を幅広く把握します。加工現場は GTDA を導入することで、どこで工具の性能を向上すれば生産性を向上できるのかを知ることができます。また、工具関連の問題によって、製造フローにおける時間とコストを浪費するボトルネックが発生している可能性がある箇所を発見することができます。
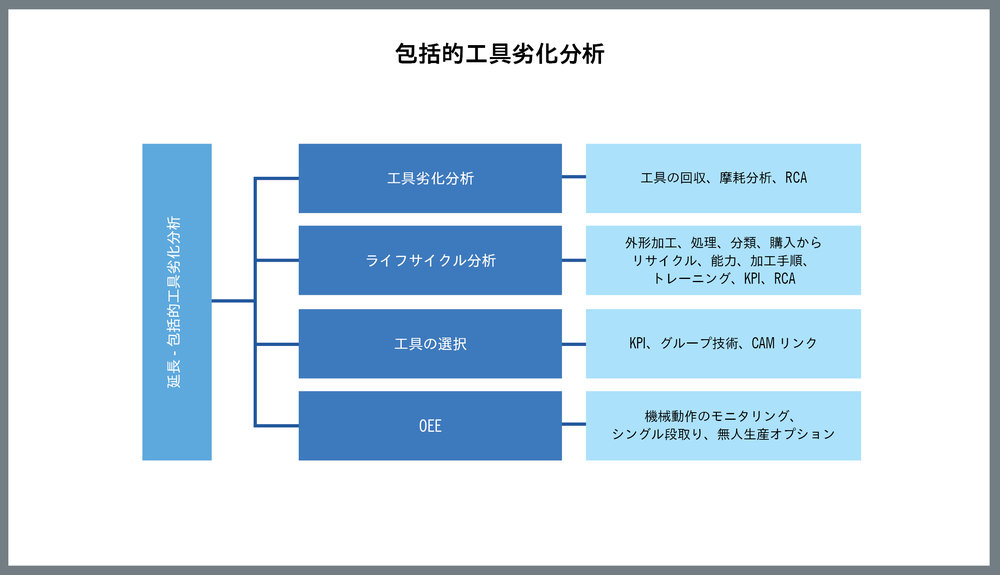
工具劣化に関する分析
図 7
セコ・ツールズのコンサルティングサービスは、GTDA の具体的なテーマについて、『Tool Deterioration: Best Practices(工具劣化: ベストプラクティス)』というタイトルのテキストを作成しています(図 8)。このテキストでは、工具劣化は被削性モデルのバランスポイントであり、機械加工工程のほとんどの問題は、工具劣化に関連する事象として分類できるとしています。また、金属切削におけるさまざまな用途について検討し、工具劣化の原因となる現象に関するインサイトを紹介しています。さらに、工具劣化が発生する工程を確認して対処し、制御する方法に関する「ベストプラクティス」を概説しています。
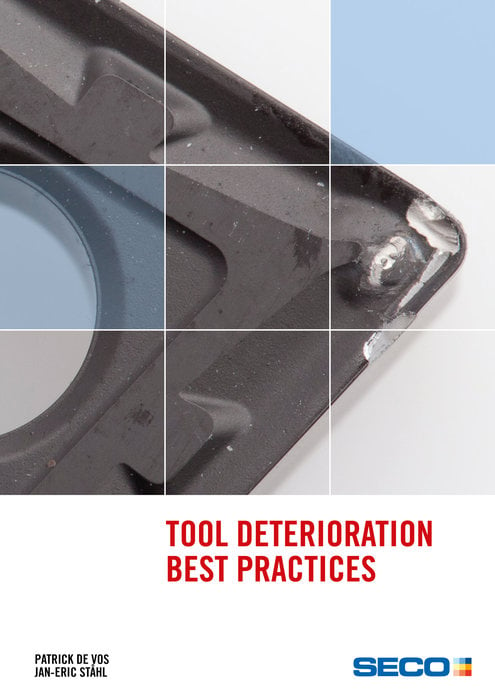
工具劣化の制御方法2014
図 8
著者:
セコ・ツールズ全社技術教育マネージャ、Patrick de Vos