www.engineering-japan.com
18
'17
Written on Modified on
製造業における無駄の実践的な管理法
メーカーは、最高の生産性と効率を達成できる方法を常に求めています。 現在こうした取り組みには、近頃流行りのクラウドコンピューティング、データ駆動型製造、サイバーフィジカルシステム、インダストリー 4.0 などを採用した高レベルのプログラムが取り込まれることが増えています。こうした先進的な取り組みは優れたコンセプトであり、目覚ましい成果を達成する可能性がありま す。しかし、実際の製造現場ではこのような意欲的な計画実行が阻害されており、製造工程では無駄が管理されていないのが切実な現状です。
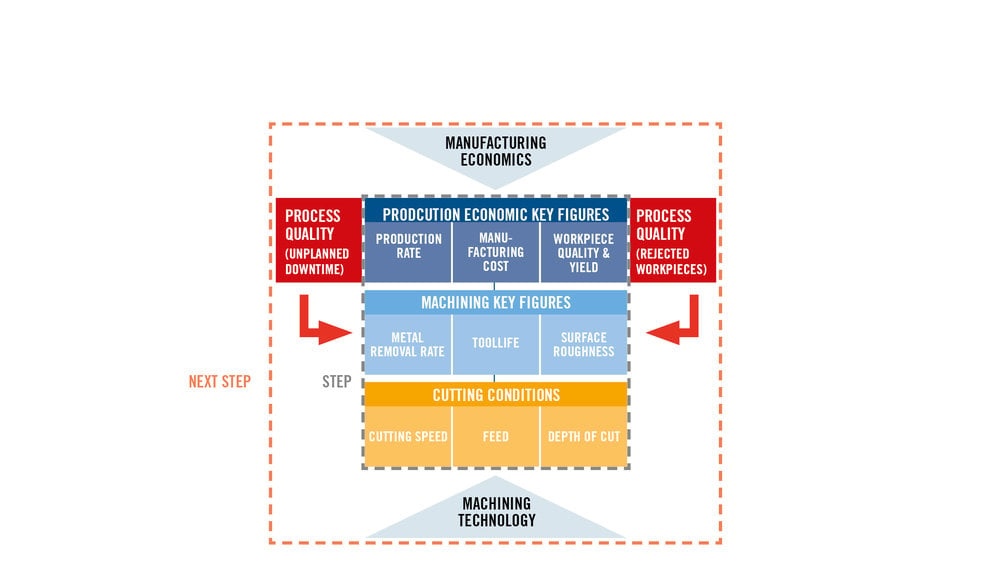
し、無駄を削減または排除する方法を策定する必要があります。メーカーが最先端のスマート製造戦略を採用する準備を進めるうえで、無駄の管理が第一歩となります。
図 1 – 製造工場の全要素および相互関係と作用を示す全体図(NEXT STEP モデルとコンセプト)。
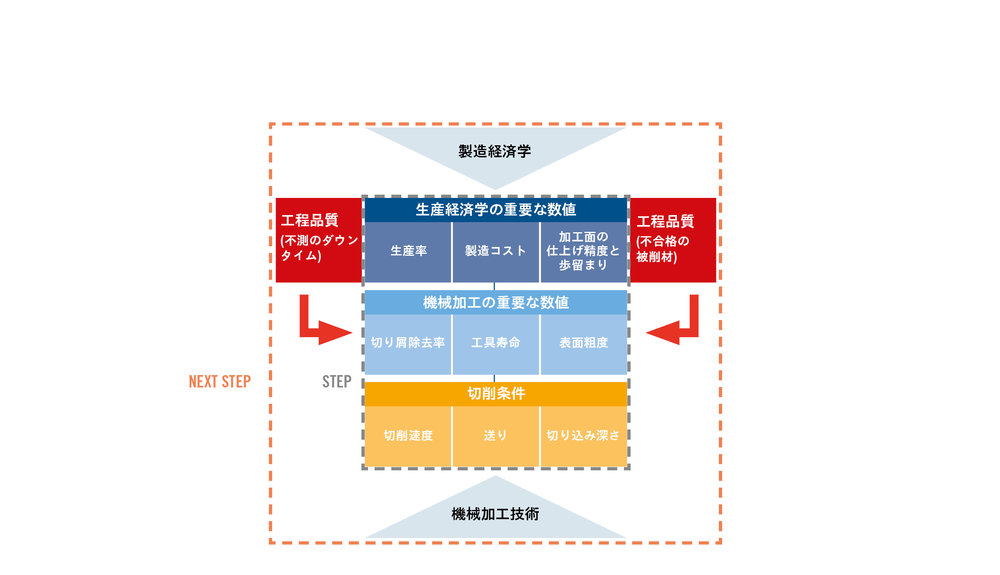
生産経済学の基礎
製造とは、連続した変換工程で構成されます。生産現場では、鍛造、溶接、機械加工など一連の変換作業を通じて、原材料から仕上げ/中仕上げ被削材を形成します。各作業は、多くの要素で構成されています。たとえば、機械加工には切削工具、工作機械、材料固定具、クーラント供給などの基本要素があります。これらの要素に関連の工具と生産システム部品が組み合わされて、機械加工システムが構成されます。
生産システムの周辺には、計画、プログラミング、経済的な管理などの機能があり、これにより生産環境が形成されます。生産環境で、重要な要素は人です。現在、製造にはコンピュータ、ロボット、その他の先端技術が広く利用されていますが、環境全体の管理に関する意思決定をするのは人です。
機械加工工程は、ツール選択、切削条件、プログラミング、被削材種、材料固定具に関する詳細な技術的適用に基づきます。このほか、生産量要件や指定された加工面の仕上げ精度などの重要な詳細があります。
詳細な技術的適用を経済的課題と関連づけたものを生産経済学と呼びます。生産経済学では、関連する要因すべての最適なバランスを達成することを目指します。技術的要素で加工面の仕上げ精度、数量、適時性に望ましい成果を達成すると同時に、経営では事業存続を実現するコストを重視する必要があります。
機械加工工程では、3段階で生産量とコストのバランスを調整します。第1段階では、信頼性の高い機械加工工程を確立します。ここでは、工具の破損、制御されない切り屑、切り屑による被削材種の損傷などの不測の事態を最低限に抑えることが重要です。加工現場では、機械加工工程で発生する機械的負荷、熱負荷、化学的負荷、摩擦的負荷に対応する、またはこれを上回る耐負荷能力のある工具を選択して、作業の信頼性を確保しています。
図 2 – STEP で開発された全体的な製造可能性モデル。
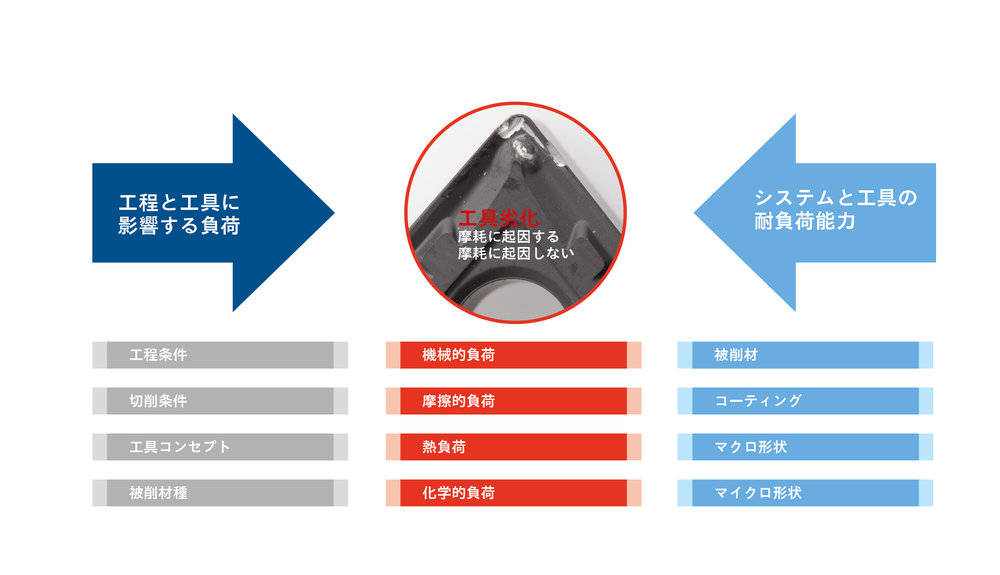
HQ ILL 製造可能性モデル
生産経済性のバランスを確立する第2段階では、実際の生産状況で機械加工工程に適用する制約に応じて切削条件を選択します。切削工具は、理論的には広範な能力を持ちます。しかし、実際の加工現場では、有効な適用パラメータ範囲が制約されます。
例えば、加工に使う工作機械の出力、被削材種の加工特性、振動や変形しやすい部品構成などにより、工具の能力や性能にばらつきが生じます。理論的に有効な切削条件は多数ありますが、実際の生産環境には制約があるため、問題の発生しない選択肢は限られます。
図 3 に切削速度、切り込み深さ、送りの選択肢を示しました。多くの選択肢がありますが、実際の切削適用を考慮すると、選択肢が狭まったり、数が減少していることが分かります。
図 3 – 切削環境の制約内で採用できるすべての切削条件の組み合わせを示した 3D 図。
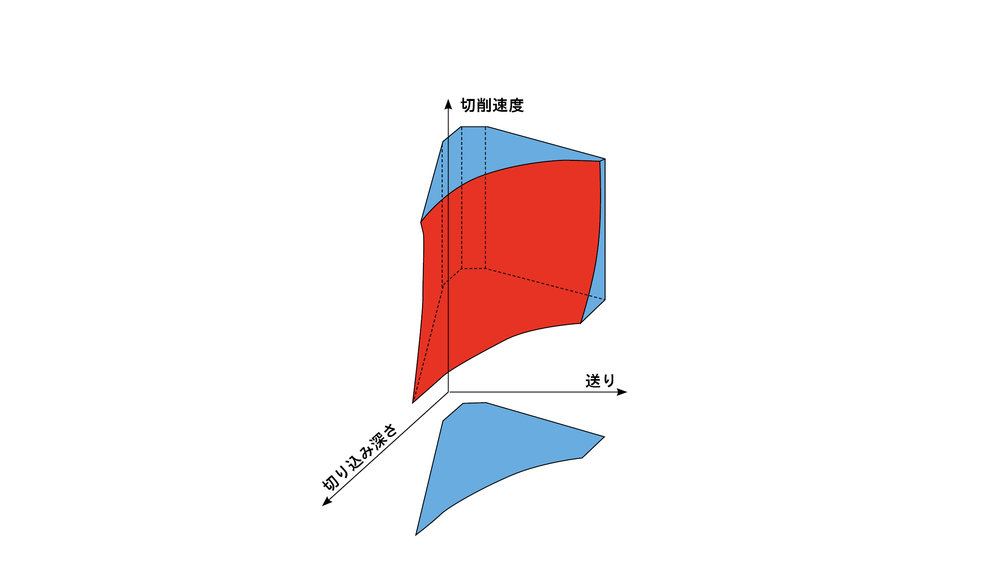
実際の状況の制約に対応しない切削条件を適用すると、コスト増、生産性低下など、経済的にマイナスの結果が生じます。機械加工時に発生する問題の約 90%は、実際のワークショップで生じる切削工程の制約を
無視したためと考えられます。
切削条件が、実際の加工現場の制約を超えなければ、技術的には安全に作業できます。ただし、技術的に安全な切削条件は、必ずしも経済的に優れているとはかぎりません。切削条件が変わると、機械加工工程のコストも変わります。よりアグレッシブな切削条件でも技術的に安全性を確保できれば、仕上げ被削材の生産量は増加しますが、アグレッシブな切削パラメータでは工具寿命が短縮されるため、ある時点を超えると生産性が低下します。摩耗した工具の交換に時間がかかるため、部品生産量も低下することになります。
生産量と製造コストをバランスよく達成できる切削条件の組み合わせがあるはずです。図 4 には、切削条
件、生産性、工具/加工機械コストの関係が示されています(グラフでは、切削条件の変化に伴って変化する要素のみを示しています - 材料費、間接費、管理費、エンジニアリング費は含まれていません)。軸の右に行くほど切削条件がアグレッシブになり、軸の上に行くほど生産性が高くなります。グラフ中央に薄い青で示した帯は、切削条件が生産性(最大の生産量)と経済性(最低のコスト)をバランスよく達成する範囲を示しています。
図 4 – 切削条件、生産性、機械加工コストの関係。これは簡易モデルで、無駄の要因は考慮していません。
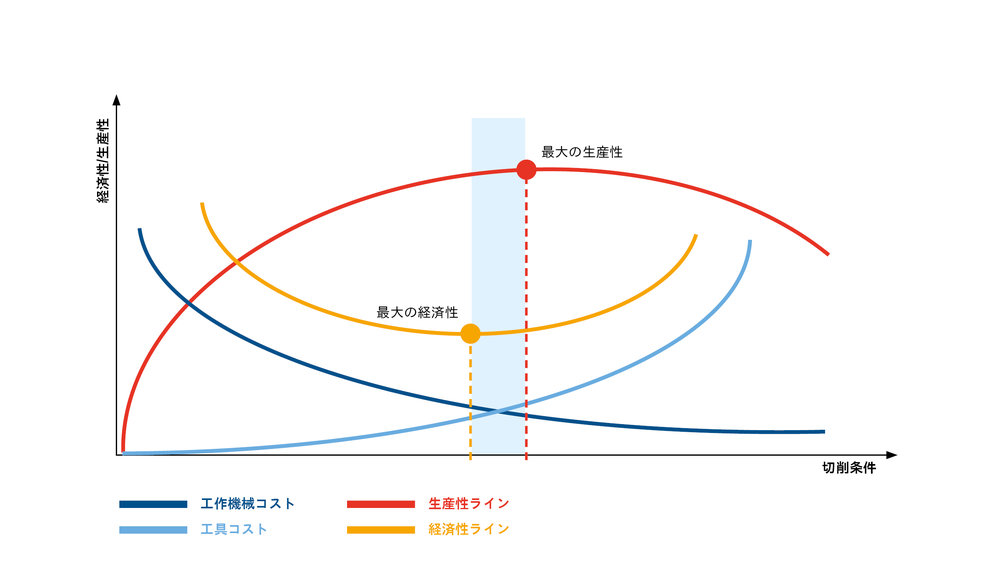
HQ ILL 機械加工 切削条件 生産高 機械加工コスト
次に、生産性と経済性をバランスよく達成する第3段階では、状況に応じて最適の切削条件の組み合わせを決定します。機械加工作業の全要因を考慮して、生産性と経済性を望ましいバランスで達成する切削パラ
メータの作業ドメインを決定することが重要です。
生産経済性に与える無駄の影響
残念ながら、バランスに優れた生産経済学の科学的方法を採用したとしても、製造システムの無駄により効果が左右されます。無駄によりバランスが崩れ、様々な影響が生じます。たとえば、わずか 15kW しか必
要としない日常的な用途に 60kWの機械加工工具を使った場合、エネルギーと電力が無駄になります。別の状況では、仕上げ被削材が求められる品質レベルに達しないと、不合格品のために工程につぎ込まれた時
間、費用、リソースが無駄になります。同様に、必要以上の品質レベルで被削材を製造することも、高い品質ほどコストがかかるため、無駄が生じます。
無駄があまり目につかず、認識しにくい状況に、知的資源の活用不足や誤用があります。会社内に目標達成に貢献する知識やスキルを持つ人材が存在しても、社内方針や不十分なコミュニケーションなど様々な理由で、その知識やスキルが共有されずに無駄になってしまう場合があります。
無駄削減ツール
無駄を特定、分類してから、生産現場では無駄の削減/排除計画を策定する必要があります。メーカーが無駄の多い慣行を正確に特定し、定量化し、最低限に抑えることができるツールは数多くあります。例えば、工具の活用度、操作、劣化を分析することにより、問題のある領域を明確化できます。
このような分析では、摩耗と判断された工具のうち 20~30%もまだ使える状態であることが示されています。この場合、残りの工具寿命が無駄になります。工具の摩耗基準を明確にし、その基準を現場にきちんと伝えることで、工具寿命の無駄を大幅に省くことができます。
同様に、加工機械のダウンタイム分析では、設定、プログラミング、工具交換に費やした時間を定量化します。これらの分析によると、必要ではあるが時間のかかる活動をより良く把握したうえで、実行、調整することで、機械のダウンタイムを 50~60%も削減できることを示しています。
面談、調査、トレーニングプログラムを活用すると、知的資源の無駄、知識とスキルの認識不足につながる人材に関する問題に対処するのに有効な情報が明らかになります。その結果、従業員がより良く業務を実施できるようになり、個人の生産性を最大限にまで高める能力を開発できます。
価値付加活動、価値実現活動、不要な活動の管理
20世紀初頭、米国の生産技術者 Fredrick Taylor は製造現場の作業を調査し、最終製品に付加価値を提供しない活動を工程から排除することによる、生産性改善を提唱しました。現代の「リーン」製造ガイドラインは、この考え方の延長線にあります。
機械加工作業では、工具が実際に金属を切削して、切り屑が発生している場合のみに、真に付加価値のある活動が発生しています。部品の機械への取り付けや固定など、その他の活動は価値実現活動と呼ばれ、生産品に直接価値を付加しませんが、価値付加活動を実現するために必要です。
機械加工システムの3番目の活動グループは不要な活動です。これらの活動は価値を創出しないばかりか、価値創出を支援するのでもなく、リソースを消費するばかりで、利点をもたらしません。これこそまさに無駄です。問題解決は、不要な活動の一例です。そもそも最初の段階で工程が適切に設計および管理されていれば、問題は発生せず、問題解決に時間を無駄にすることもありません。
図 5 – 機械加工現場と関連する全要素の概略図。
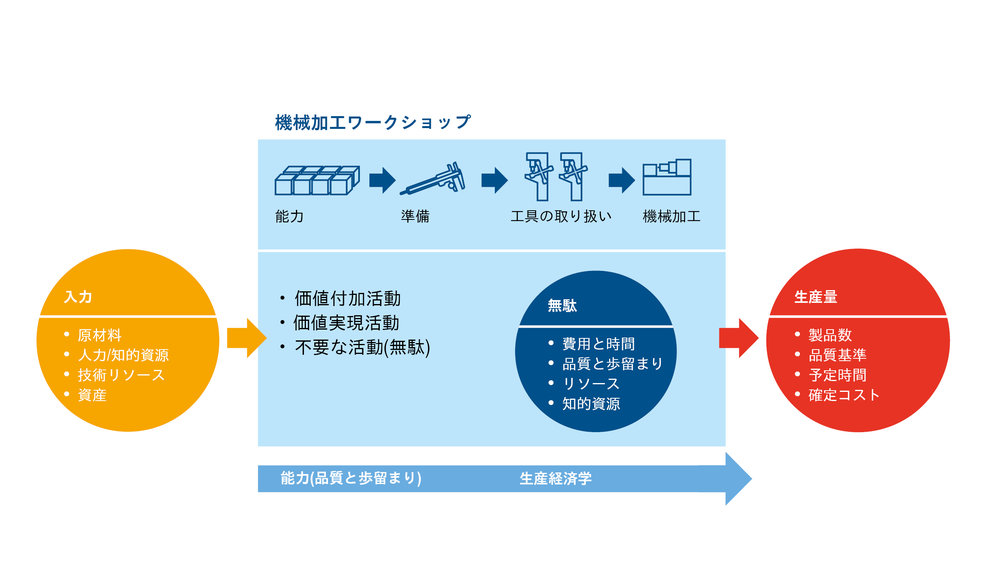
HQ ILL 機械加工現場
結論
過去においては、不要な活動は製造工程の一部として許容され、バランスに優れた生産経済性の達成を大きく阻害する要因とは認識されてきませんでした。現在では、不要な活動を排除または最低限に抑制する方向が注目されています。生産性または生産量計画では、不要な活動を排除し、価値実現活動を最低限に抑制
し、価値付加活動を最適化することが重視されています(図 6)。
図 6 – 価値付加活動(オレンジ)、価値実現活動(青)、無駄な活動(赤)。人的要因(グレー)は、最高の製造
パフォーマンスを最適に達成するのに重要な要因です。
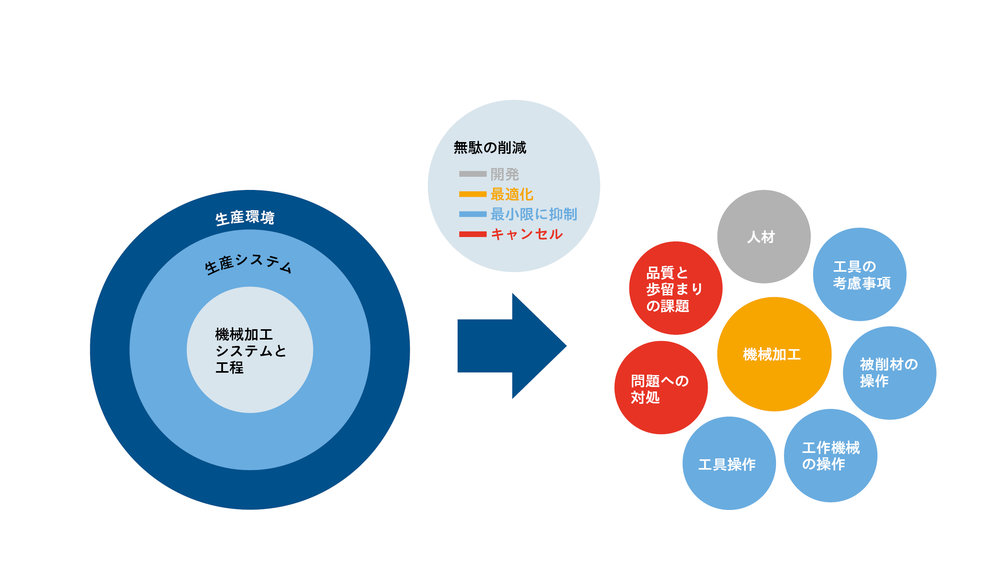
HQ ILL 機械加工工程システム
無駄を省くと、理論上の生産経済学が、実際の生産経済学となります。ここまで生産経済学が進展すると、会社の成功に直接貢献できるようになります。ただし、無駄を全面的に排除しようとする際には、注意が必要です。重要なのは、無駄の削減活動の費用対効果を定量化することです。無駄の発生を全面的に排除するためには多額の投資を伴うことがあり、経済的な観点では、無駄を許容する、部分的に削減する、または共存する方が賢明な場合があります。こうした意思決定は、適切な定量分析をしたうえで、会社の目標や理念への影響を社内で検討してから実施すべきです。
補足:
セコ・ツールズのコンサルティングサービス
製品の製造が高度になるほど、新しい技術を最大限に活用するために、アプリケーションの支援がますます必要になります。機械加工では、初期レベルの支援として、特定の作業に最適な工具選択のアドバイスを提供します。工具の選択後、さらに詳しい情報を得ることができれば、最適な切削条件、クーラントの使用、その他の考慮事項を選択しやすくなります。その後、工具が期待通りの機能を発揮しなかった場合、工具サプライヤよりトラブルシューティングが提供されます。以上の 3つの方法での支援は、従来の工具
サービスの構成要素です。
工具サービスが拡張して単一の用途から工程全体を網羅するようになり、1台~複数の工作機械での、複数の作業で加工作業を実施する場合における、最高の効率と生産性を実現するための、作業順序、被削材操
作、その他の要因についての、エンドユーザーへの指導。このレベルの支援は、エンジニアリングサービスと呼ばれます。
近頃では、メーカーは加工現場や組織全体で機能、生産量、コスト管理の改善がますます求められるようになっています。このような場合、独立系のコンサルティング会社が管理または製造コンサルティングを提供します。ただし、製造組織を実際に評価するには、中核事業の全面的な理解が不可欠です。
セコ・ツールズはその機械加工工程と工具に関する長年の幅広い知識を適用して、従来型の工具サービス、エンジニアリングサービス、包括的なコンサルティングサービスを数十年にわたって提供してきました。各サービスは緊急時対策、または状況に応じて提供されてきましたが、2016年、セコ・ツールズはコンサルティングサービス部門を設立して、さらに効率的で即答性に優れた製造サービスを幅広く提供しています。
セコ・ツールズのコンサルティングサービスには、幅広い専門リソースと提供方法があります。ツール選択と用途に関する支援については、オンラインで 24時間利用することが可能で、製造現場での生産性のニー
ズに即座に対応できます。
エンジニアリングサービスは、まずオンラインのやり取りで対応し、必要に応じて現場を訪問します。セコ・ツールズのコンサルティングサービスでは、ワークショップでの各機能の操作に関する包括的な分析とガイダンスも提供しています。このサービスには、工作機械のメンテナンス、ワークショップのレイアウト、物流、組織的な機能に関するコンサルティングも含まれています。人材スキルや知識の問題に関するアドバイス、組織の生産戦略に採用される製造技術との関係、コスト面での考慮事項もサービスの一環として提供いたします。
セコ・ツールズのコンサルティング関係は NEXT STEP コンセプトをベースとしますが、メンバー組織の個別のニーズに応じてカスタマイズも可能です。さらに、セコ・ツールズとお客様が共通の目標達成に向けた話し合いをすることも可能です。