www.engineering-japan.com
04
'20
Written on Modified on
レーザー技術を使用したハイブリッド製造のマイルストーン(中間目標)
KUKAは、ドイツ連邦教育研究省(BMBF)によるカールスルーエ工科大学(KIT)への支援プロジェクトにおいて、フラウンホーファー研究機構レーザー技術研究所(ILT)等の産業パートナーとともに、ハイブリッドなLMDテクノロジーの生産チェーンへの統合に取り組んでいます。そこに導入されるのが、3Dプリントとしておなじみのレーザーメタルデポジション(LMD)方式です。その設備のベースをKUKAロボットが構成します。
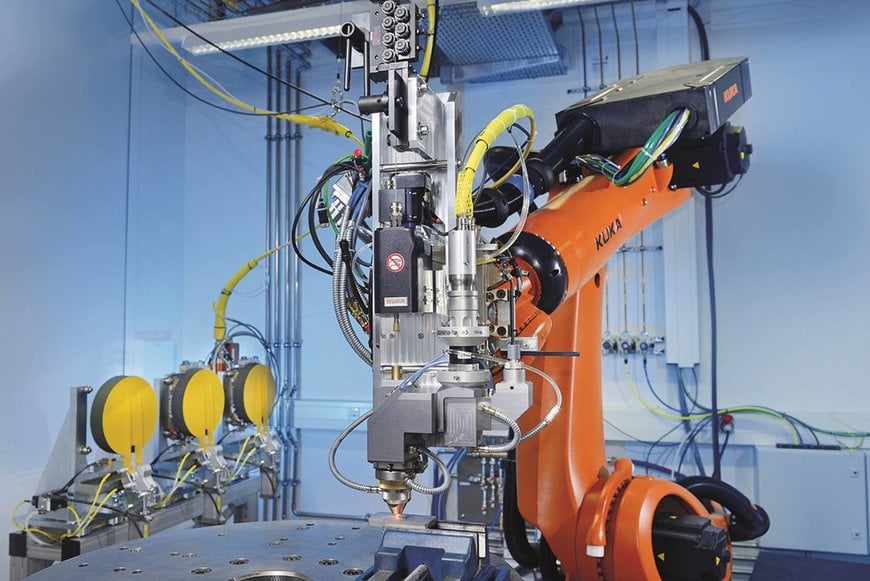
製造工場では、従来型のサブトラクティブ法が未だに標準となっています。その際、複雑な形状の構成部品の鍛造および鋳造には、多くの場合、高額の加工コストを余儀なくされます。例えば航空機用の高性能で軽量な部品を製造する場合、依然として原材料の最大90パーセントが無駄になっています。これに対して、積層造形では、構成部品が層状に積み重ねられます。これにより資源の節約や産業廃棄物の削減のみならず、極めてフレキシブルな製造が実現されます。
実用的な代替方法としてのハイブリッド積層造形システム
従来の方法に替わる実用的な方法がハイブリッド積層造形です。この場合、鍛造や鋳造など従来の方法で製造されたブランクに、積層造形を加えて複雑な形状に加工することによって、オーダーメイドの構成部品になります – 例えば、ドイツ連邦教育研究省(BMBF)による支援プロジェクトであるProLMDにおいてはレーザメタルデポジション(LMD)法が使用されます。もう一つの積層テクノロジーのメリットは、高効率製造です。例えば航空機用の部分補強済み構造部品やタービン用の高機能部品を効率的に完成することができます。従来は往々にして高コストの上に加工条件の要求が高かったために、この技術を広範囲に使用することはできませんでした。
"レーザーメタルデポジション法では、材料の酸化を防ぐため設備全体を保護ガス内に設置します。従ってどうしても加工する部品のサイズは制限されてしまいます。"
ギュンター・ノイマン、KUKAレーザーアプリケーション事業部責任者
KUKAレーザーメタルデポジション(LMD)法に基づく大型部品のハイブリッド製造システム
ProLMDプロジェクトの目標は、大型部品の製造時にLMD法を適用するために、堅調で高効率の処理技術とシステム技術を開発することです。このシステムは、航空・宇宙といった分野で、最新の技術と高い安全要件を満足します。KUKAロボットをベースに標準化されたシステム技術は、低コストというメリットを提供します。ファイバーガイドシステムを使用することにより、ロボットの作業領域はほとんど無制限です。そのため、ロットサイズが小さい場合でも、部品の形状や大きさにフレキシブルに対応することができます。
レーザーメタルデポジション(LMD)のメリット:製造時間の短縮、低コスト
ProLMDの研究成果は、来年以降プロジェクトパートナーであるMTU、Airbus、Daimler各社の生産に導入されることが既に決まっています。「わが社は、ハイブリッド製造方法の産業転換を示すマイルストーン(中間目標)から踏み出しています」と、KUKAProLMDプロジェクトリーダーであるラルス・オットーは言います。専門家たちは、この技術によって製造時間を50%短縮し、コストを20~30%削減するという目標をクリアしています。さらには、その実現によって、製造時の生産資源効率にも持続的に貢献することができます。
KUKAは、このプロジェクトにおいて、ロボットベースのレーザー技術分野においてアーヘンの専門家たちが長年にわたって築いてきた経験を拠り所としています。このプロジェクト向けに、KUKAはハイブリッド積層造形用の同一の生産ラインを二基設計しました。それらはアーヘンのヴュルゼルンにある当社工場とその近郊にあるフラウンホーファー研究機構で既に稼働しています。「長期的には大量生産向けの方法を吟味するつもりです」と、ギュンター・ノイマンは説明します。
www.kuka.com