www.engineering-japan.com
08
'19
Written on Modified on
3D印刷 - Eモビリティ工具の未来
ケナメタルが開発した3D印刷によるステーター内径加工用軽量工具は、精度、真円度、表面仕上げの要件を満たします。
ケナメタルは、ハイブリッド車や電気自動車向け部品の加工に使用されるより軽量のツーリングソリューションに対するお客様の需要の高まりに対応できるよう、特別に設計された3D印刷によるステーター内径加工用工具を開発しました。
Eモビリティ部品は通常、より軽量のツーリングソリューションを必要とする小型で所要動力の低いCNCマシニングセンターで加工されます。ケナメタルの3D印刷によるステーター内径加工用工具は、従来の工具の半分の重量でありながら、アルミニウムモーターボディの穴開け加工に対する精度、真円度、表面仕上げの要件を満たします。
「電気モーターのステーターを囲うメインボアの直径は約250 mm(9.84インチ)、長さは約400 mm(15.74インチ)で、底部にはより小さなベアリングボアがあります」と話すのは、プログラムエンジニアリング担当マネージャーのHarald Bruettingです。「従来の方法で製造する場合、この種のアプリケーションに使用するリーマの重量は25 kg(55ポンド)を超え、既存の工作機械や工具を使用して作業するオペレーターには重すぎます」。
Bruettingとケナメタルのソリューションエンジニアリンググループは、その積層造形能力により、高精密仕上げ用の細かい調整が可能なRIQリーマインサートや最大の剛性を実現するKM4Xアダプターなど、ケナメタルの実績ある技術を取り入れた3D印刷による堅牢かつ軽量のスローアウェイツールを完成させました。この工具はまた、生産性と工具寿命を最大化させる3D印刷による内部クーラントチャネルを特長としています。
「金属粉末床3D印刷を有限要素解析ソフトウエアと使用することで、慣性モーメントをスピンドル面に非常に近づけた工具を設計・製作し、工具の重量を考慮しながら剛性を向上させることができました」と、フューチャーソリューション担当マネージャーのWerner Penkertは言います。「これは、お客様固有の課題を解決するために、ケナメタルがいかに先進の製造技術を取り入れているかを示すよい例です」。
炭素繊維チューブを使用した工具と3D印刷による金属チューブを使用した工具の2種類が製作されました。結果は目を見張るものでした。3D印刷によるチューブを使用した工具の重量は10.7 kg(23.6ポンド)、炭素繊維が使用された工具の重量は9.5 kg(20.9ポンド)で、従来の工具の半分以下です。
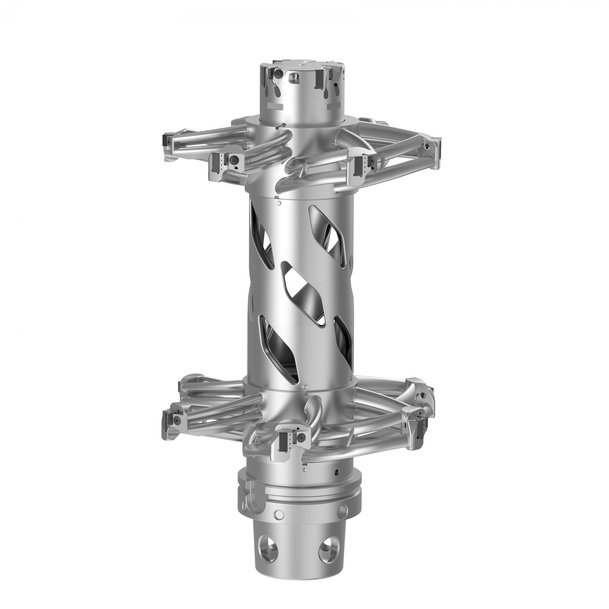
ケナメタルの実績ある技術の使用。高精度RIQリーマインサートと実現可能な最高の剛性を達成するKM4Xアダプター。
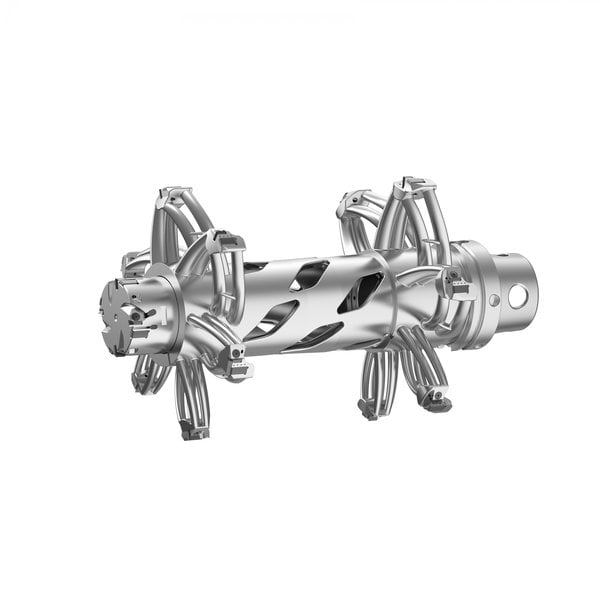
積層造形による軽量化。3D印刷、総重量は10.7 kg。重量を半分に軽量化し、ステーター内径に対する表面品質、真円度、精度に対する要件をクリア。
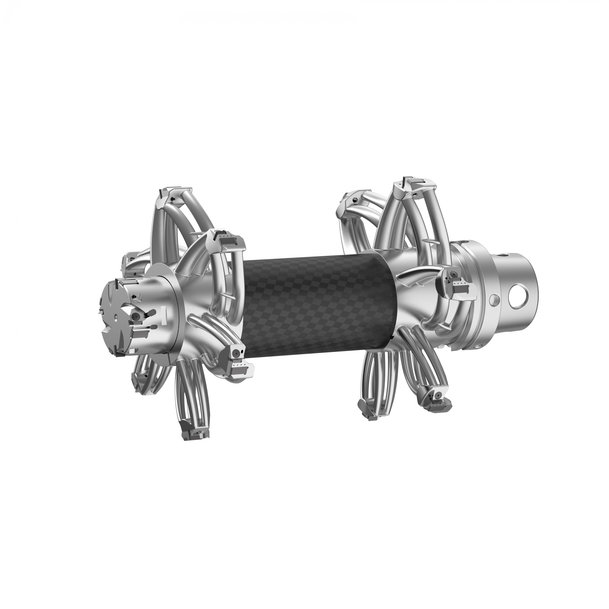
同じ工具をさらに軽く。3D印刷による金属チューブの代わりに、炭素繊維チューブを使用した工具を採用。さらに9.5 kgまで軽量化。